10 Benefits of Internal Inspections for Suppliers
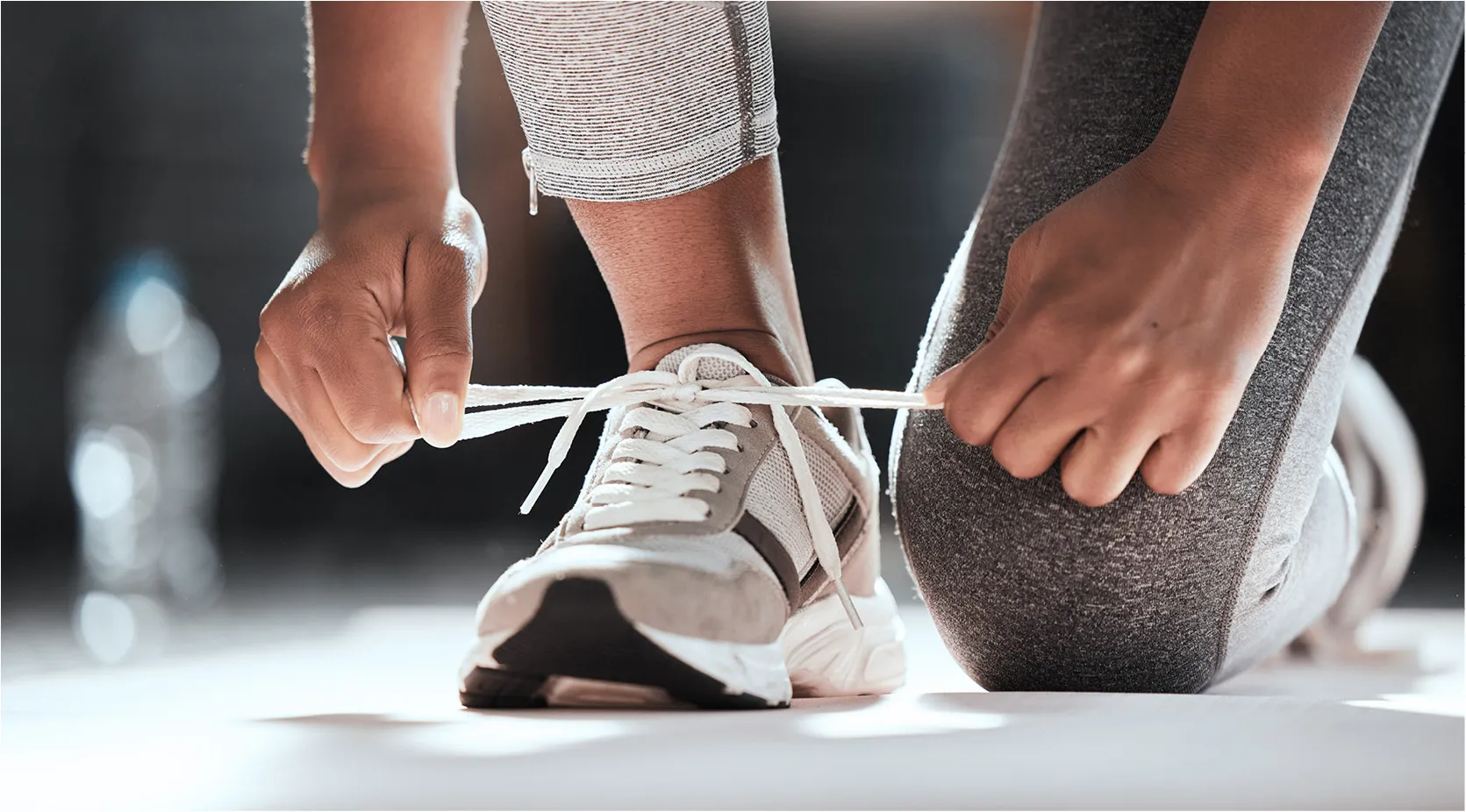
What are internal inspections?
Internal inspections allow you, as a vendor or factory, to customize and manage your own internal quality operations. You can set up your own quality protocols, defect classification lists, inspection workflows, reports, and more to meet your specific requirements. By monitoring quality and performance in-house, you can better control your processes, catching and eliminating problems before they become visible to the retailer or brand.
What is the difference between self-inspections and internal inspections?
The main difference between self-inspections and internal inspections is that, with self-inspections, you execute inspections for the brand or retailer based on their quality criteria and share the reports as required. On the other hand, internal inspections are conducted by you as a vendor or factory, following your own pre-configured quality standards. You have the autonomy to execute your inspections and choose to share the results with your customer, or not.
Top 10 benefits of internal inspections
1. Save costs
Internal inspections are highly cost-effective compared to traditional third-party inspections, resulting in significant cost savings for suppliers. By using your own resources and expertise, you can avoid the expenses associated with external inspections, such as travel costs and inspection fees.
A digital quality management platform can eliminate manual work and tedious Excel sheets with auto-generated inspection reports, increasing efficiency while saving time and money.
2. Deliver consistent-quality goods to your buyers
The use of digital tools to perform internal inspections help you gain visibility into the performance data of all your factories. By quickly identifying which factories are underperforming, you know where to put resources to get them back up to quality standards. When you’re consistent with the quality of your products, you build trust with your buyers and increase their level of satisfaction.
A digital platform enables better data management and internal inspection analysis, both of which provide further visibility into problem areas. Digital and collaborative corrective and preventive actions (CAPA) drive real actions improving quality with each production run. When you fix problems at the source, you save on expensive return cycles.
3. Improve awareness of product requirements
When quality is managed internally via self-inspections, standards, and requirements are much clearer to all parties involved in the production of goods. This keeps errors low and quality high, which is a key ingredient for lowering overall costs and keeping your buyers happy.
Pre-production meetings (PPMs) and CAPA are two valuable elements of this process — and with a digital solution, you can seamlessly connect all stages of production, from pre- to post-production activities, while monitoring quality at all stages.
4. Enhance trust and satisfaction with your buyers
As a supplier, you want to use internal inspections to show your buyers you are reliable and can deliver the best quality products.
When you perform internal inspections with the right technology tools, you can share the results of those inspections with your buyers – showing them the state of the quality of their products at every stage of production. This can increase trust and satisfaction since your buyers have visibility over your production processes. The best part is you don’t have to pay a third-party agency to do this.
When your inspections consistently align with results, both sides gain trust. With trust comes better cooperation and more fruitful partnerships.
5. Become more agile
COVID-19 revealed the fragility of supply chains. Restricted mobility prevented third-party inspectors from entering factories, resulting in compromised product quality and lengthy shipping delays.
In the face of these major disruptions, only those who pivoted to setting up internal quality workflows could continue production.
Building up your internal quality program with internal inspections allows you to respond more quickly to changes in the environment and gain visibility into key areas of your business at all times.
6. Foster a greater level of accountability
When you are accountable for the quality of your own products, you open the door to strategic relationships with brands and retailers.
Having an internal quality program in place allows you to establish a greater degree of trust and transparency that customers are looking for today. By proactively addressing any issues that arise and quickly addressing them in an organized way, you will gain the trust of customers.
Real-time visibility into product quality metrics also allows you to better understand your weaknesses and strengths in terms of meeting customer expectations, which can help you target areas for improvement.
7. Achieve higher returns with your internal quality program
By implementing an internal quality program, you can improve the returns on every product that is produced. When products meet or exceed customer expectations, it leads to higher customer satisfaction and repeat business.
A digital platform can standardize your internal inspection processes so you can collect data on product quality more frequently than with third-party inspections. This data can then be objectively compared to the product quality metrics set by your organization to measure and improve product quality over time.
8. Optimize your operational processes
Centralize your quality activities by bringing all your quality teams and factories onto the same digital platform. Communicate quickly and easily between teams, factories, and inspectors with real-time updates and shared reports. You can schedule inspections without worrying about time-zones or language barriers, keeping production lines running efficiently. Your inspectors can generate reports in just seconds with a user-friendly mobile app, saving time and eliminating the need for manual report writing.
The results of this are significant savings across a company’s revenue, including:
- 100% time savings on internal report generation
- 19% decrease in the defective unit rate
- 80-90% time savings in corrective interventions
- 50% improvement in risk mitigation
9. Make more informed decisions
A digital platform automatically collects and analyzes information on quality, identifying trends and sharing insights that previously would have required a team of data analysts. This gives you a 360º view of your company’s quality performance, no matter how complex your production network is.
This lets you base your decisions on data, identify gaps, calibrate performance using KPIs, and proactively manage your self-inspection program to fix problems before they occur.
10. Create a culture of empowerment and continuous improvement
Build a culture of quality across your organization, creating high standards of accountability, empowerment, and visibility needed for continuous improvement. With a digital platform, your teams can easily track and share progress, driving excellence across the organization. Everyone can learn from the successes and failures of past projects, allowing better decision making and smarter strategies for the future.
Conclusion
Implementing an internal inspection program is a faster and easier process when you have the right platform to support it. Modern quality platforms like Inspectorio to help suppliers scale quickly and efficiently while maintaining high standards of accountability, visibility, and quality.
You can improve processes that are central to your organization’s revenue by:
- Reducing your reliance on third-party inspections.
- Standardizing operations across your inspection teams.
- Aligning internal quality control personnel on what to look for.
If you’re looking for a platform to improve your internal inspection processes and gain visibility into production and factory operations – both locally and globally – Inspectorio can help. Contact us today.