The Future of Supply Chains is Digital Collaboration

Data is key to the efficient operation of supply chains. Using a system that results in quality data and actionable leads results in quick problem solving and business improvements.
But just having data isn’t enough. For maximum results, that data also needs to be shared with and used by every stakeholder in the supply chain.
Recently we sat down with Coresight Research and two Inspectorio clients to discuss how digital collaboration enables true ownership, saves money, and empowers growth. Data is key to the efficient operation of supply chains.
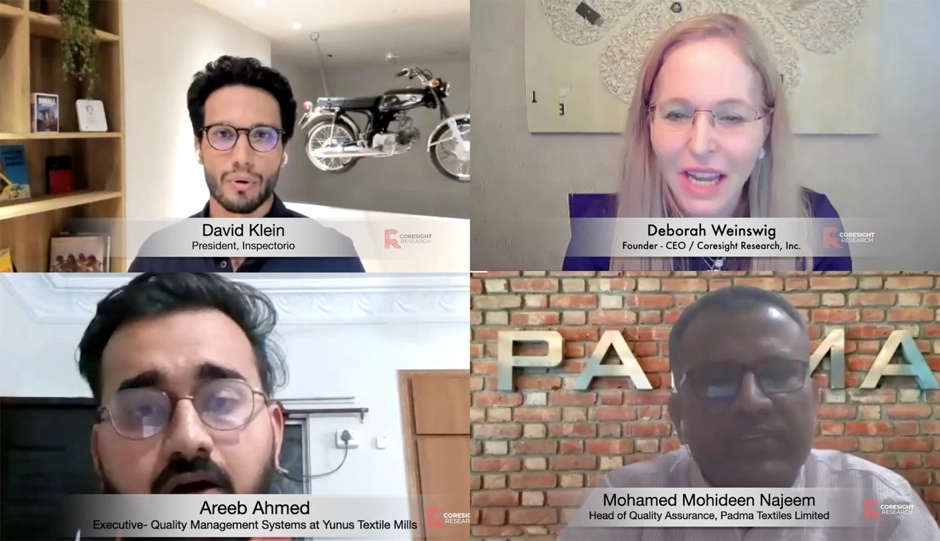
How the pandemic empowered supply chains
Using a system that results in quality data and actionable leads results in quick problem solving and business improvements.
But just having data isn’t enough. For maximum results, that data also needs to be shared with and used by every stakeholder in the supply chain.
Recently we sat down with Coresight Research and two Inspectorio clients to discuss how digital collaboration enables true ownership, saves money, and empowers growth.
In a roundabout way, the pandemic showed supply chains exactly what they were capable of.
Before the pandemic, the idea of a company’s supply chain operating remotely seemed almost impossible. But companies quickly realized that it was possible – with the right digital tools.
“As brands and retailers, vendors, factories, all make this realization, they are starting to go to systems, platforms that actually help support that and accelerate that,”
David Klein, Co-Founder and President at Inpsectorio
In addition to investing in platforms that supported business, many companies began investing in platforms that enabled communication and collaboration with their vendor and factory base.
The result is a post-pandemic supply chain that has come out the other side stronger and more empowered.
Transparency and collaboration are equally important
The use of digital platforms like Inspectorio makes data transparent for the vendors and factories who use it.
Companies who’ve made that change are taking a huge step toward greater efficiency.
But the sharing of data is just as important as having access to it.
“The biggest change is now that we do have the data, how can we make sure that all of the key stakeholders are actually looking at the data together?”
David Klein, Co-Founder and President at Inpsectorio
The goal is to create a source of truth in the form of a central data repository that can facilitate conversation and drive accountability.
Having access to centralized information and insights about performance makes it easier for factories and vendors to have a sense of ownership – and allows improvements to happen a lot faster.
When you don’t have a central platform, digitization tends to happen in silos.
“Digitization in and of itself was not enough. It’s how can we collaborate effectively together across the improvements that we now can see in a single source of truth.”
David KleinInspectorio
Digital platforms save time and money
For many businesses, switching to a digital quality assurance platform has had quick and clear benefits.
Mohamed Mohideen Najeem, Head of Quality Assurance for Padma Textiles Ltd, said his company used to do inspections manually and then organize all of the data in Excel
“Compared to the paperwork and the Excel it takes less time and expenses.”
Mohamed Mohideen NajeemPadma Textiles Ltd.
Not only are the inspections easier to conduct, but finding and analyzing the information from them is much faster.
In Inspectorio, all of the performance reports for each factory are in one place and instantly viewable.
Areeb Ahmed, Executive Quality Management Systems at Yunus Textile Mills, has had a similar experience.
Areeb said that they convinced the inspectors and workers at the factories that the transition to a digital platform would be for their own ease.
Their inspections used to take up to 1.5 hours.
“After transiting to Inspectorio, it takes 60 to 70 minutes,” Areeb said. “So, we managed to save 20 to 30 minutes per inspection. And for us, time is cost.”
Transparency improves client trust
Saving time and money is the most important factor for many businesses when moving to a digital platform, but the transparency it offers can bring even more benefits.
Areeb said that his ability to share the inspection reports with clients has led to greater client trust.
“We can now show them that we are more transparent,” Areeb said. “We are more visible. We are more traceable.”
The clients can see all of the numbers from every report.
They know which inspectors are the most competent. They see which factories need improvement.
The clients can see the numbers on every person, machine, and material.
Areeb said that enabling clients to see the data behind their processes using a single platform has transformed their factories for the better.
Client trust leads to company growth
When clients have that transparency, it fosters trust.
And when a client trusts you, they’ll give you even more of their business.
Areeb said that having a transparent business has made them stand out against their competitors.
“What makes you different is if you share your internal process with the client, if you show that how transparent your internal process is, that gains the trust of your client, helps you to make them believe that you are transparent,”
Areeb Ahmed, Executive Quality Management Systems at Yunus Textile Mills
“Your product quality is visible, your product has been passed through all the quality checks, and the numbers are there.”
Areeb shares company performance with clients on a regular basis, and invites them to tell them what they think needs to improve. They collaborate on what changes need to be made.
That transparency and collaboration increased his clients’ confidence in Yunus Textile Mills.
Their clients are now bringing them more orders.
“In the last two years, our growth has raised, our number has raised and that’s because our client trusts us and our client knows the product quality that he is going to get.”
Areeb AhmedYunus Textile Mills
Data reveals room for improvement
When you have the digitization of what were once manual processes and instant reports on performance and quality, you can make big changes much more quickly.
“The use of the platform to capture quality data can happen across your whole process of production,” David said.
And the ability to get this information immediately allows you to pinpoint which areas require attention to be able to fix those problems as fast as possible.
Mohamed has seen this firsthand at Padma Textiles.
Padma Textiles currently uses Inspectorio with six factories. When they complete an inspection, they can quickly compare it to how the other factories are performing.
“So, the less performing inspection, we can give some more effort or more concentration to improve that,” Mohamed said.
When there’s transparency and the sharing of information on a single platform, it means that vendors, retailers, and brands can work together to make swift, targeted improvements.
AI is good, but collaboration is better
In the future, supply chains will have more and more platforms to choose from that use AI and machine learning.
Those things will offer more predictive and prescriptive analyses, and that’s great.
But David said that the real future of supply chains is in collaboration.
“What will truly be a key difference in continuing to push the supply chain forward is when you look at the ability to collaborate across the network,” David said.
AI and machine learning applications will become cheaper and commoditized, but they won’t be truly effective without leveraging that data with collaboration.
Quality, compliance, and production need to be looked at holistically because they’re all part of the same facility.
“I think that is truly unlocking that ability to see everything across your different activities in the supply chain, in one place to have automation and predictability, but more importantly, this ability to collaborate efficiently and effectively,”
David Klein, Co-Founder and President at Inpsectorio
Better data and better collaboration will make for stronger businesses, improved quality, and happier customers