8 Tips to Find the Best Fabric Quality Inspection System for You
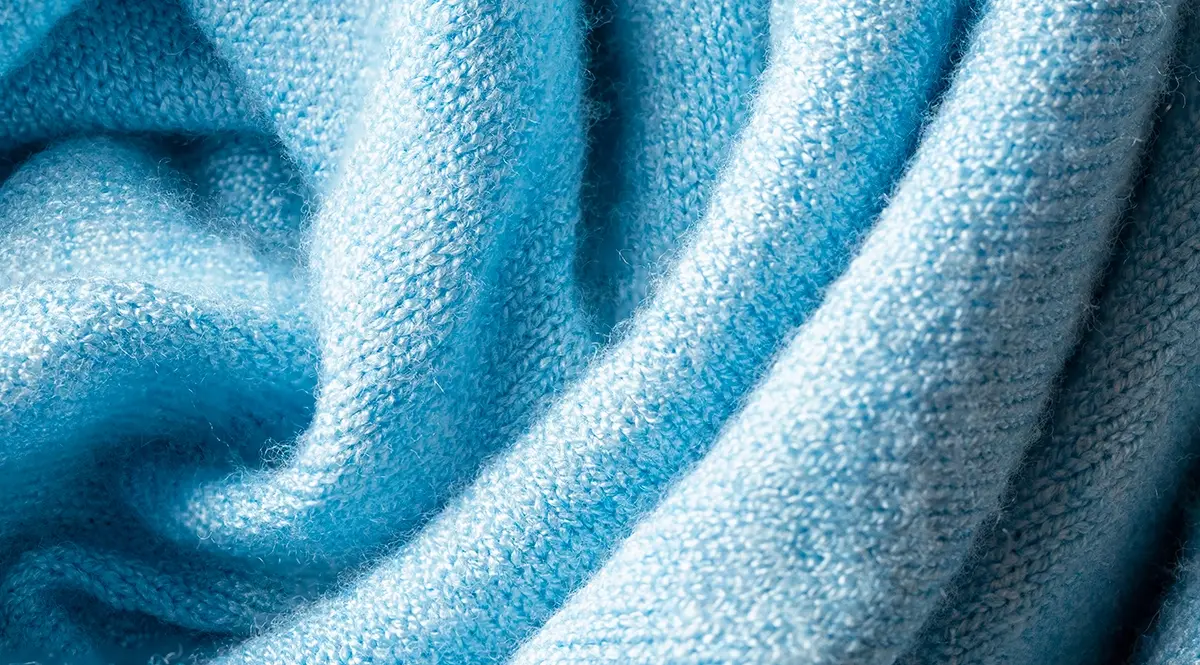
Fabric inspections are the thread that holds the garment industry together. They help to ensure that garment consistency and quality matches client requirements.
Quality issues are usually fixable when caught in the production phase — the earlier the better. When they fail to be fixed during production, minor issues at the beginning of the process can amplify into much larger issues downstream.
With fabric accounting for between 60% and 70% of all garment costs, improving fabric quality has the ability to reduce waste and save substantial sums of money.
We’re here to help you identify the fabric quality inspection system that will work best for you.
Know your quality checks
Fabric inspections are systematic observation of fabrics to ensure they meet client specifications. For instance, during the cutting phase, each cutting ticket needs to undergo a random inspection to ensure shades are separated and each part is accurately notched. If these cuts aren’t correct, they can’t be properly assembled.
Other types of common fabric defects include:
- Horizontal lines
- Uneven dying
- Drop stitches
- Neps/knots
- Defective selvage
- And more
How to identify a best-practice fabric quality inspection system
Your quality management system (QMS) needs to be digital to allow you to automate your inspection processes, customize workflows and continuously improve your operations with data analytics. Custom manual processes or your existing spreadsheets simply don’t have the functionality and flexibility.
Here are eight tips to help you find a fabric quality inspection system that can bring best-practice to your company:
1. Multiple inspection types
Configure multiple inspections types so stakeholders can verify that fabrics conform to quality standards and appearance specifications. You need to visually inspect garments at random through all stages of production, including:
- Pre-production check
- Initial production check
- During-production check
- Final random inspection
- Random sampling inspection for Acceptable Quality Limit (AQL).
2. Automated performance analytics
All defects found during an inspection, as well as the associated metrics (e.g. position, time, production batch, defect photograph), should automatically be entered into a defect log file to keep defects traceable and help to implement incremental improvements.
Additionally, analytics can provide novel insights into your suppliers and fabric mills that can inform future procurement decisions.
3. Configurable workflows
A configurable system allows you to build workflows for your different use cases and fabric types. Your inspectors should know how and what to inspect during a fabric inspection; you need to be able to easily configure standards for them to follow consistently across the supply chain.
4. Shift between online and offline use
The use of mobile devices has been revolutionary for quality inspections, including fabric inspections. Your inspectors need to be able to easily switch between their device and an online dashboard, because when they check the quality of each fabric roll, they should have the flexibility to conduct the inspection properly.
5. Document management
Proper documentation is a recurring sticking point in quality control. A digital QMS alleviates this pain by automatically storing every major activity in your quality process, along with all associated comments, amendments, metrics and other documents.
6. Data analytics
A QMS with data analytics makes your data accessible and actionable, opening up a new world of insights and objective, evidence-driven decision-making – and the right technology makes it 100% autonomous. One of the major benefits of automation in fabric inspection is continuity, because your data is trustworthy and available in real-time.
Data analytics helps to streamline the apparel manufacturing process, identify upstream potential problems, make informed business decisions, and achieve your quality assurance objectives.
7. Centralized communication
When communication is fragmented and occurs over different channels, disorganization is hard to fight off. A benchmark fabric quality inspection system centralizes all communication and collaboration between stakeholders, allowing them to monitor milestones and receive notifications in real-time. A single channel for communication also makes the process of tracking feedback efficient and helps quality inspections to go smoothly.
8. Ease of use
For your QMS to be easier to adopt and deliver value over the long term, ease-of-use is essential. This covers not just UI/UX, but training and support in the inspector’s native language. Find out how much the QMS distills the complexities of fabric inspections down to the action items, and makes them clearly available, thanks to the configurable standards shared by the brand, retailer or vendor.
Revolutionizing fabric quality inspections with Inspectorio Sight
Inspectorio Sight empowers apparel manufacturing stakeholders with previously unattainable capabilities. By revolutionizing the visibility and flexibility of fabric quality inspections, Inspectorio Sight allows you to achieve new levels of productivity and efficiency in your supply chain.
Here’s how Inspectorio Sight enables you to achieve fabric inspection best-practice:
- Configure inspection workflows and defect lists tailored to fabric requirements and use cases.
-
Centralize inspection scheduling and status tracking.
-
Execute inspections at the roll level from the Inspectorio Sight mobile app.
-
Automatically calculate scores based on the 4-point system to reduce manual work and calculation errors.
-
Access fabric inspection monitoring and reporting.
-
See analytics on fabric inspection defects and trends.
To find out how Inspectorio Sight can be the right solution for your supply chain, request a product demo today!