4 Benefits of Production Line Quality Checks and How to Optimize Them
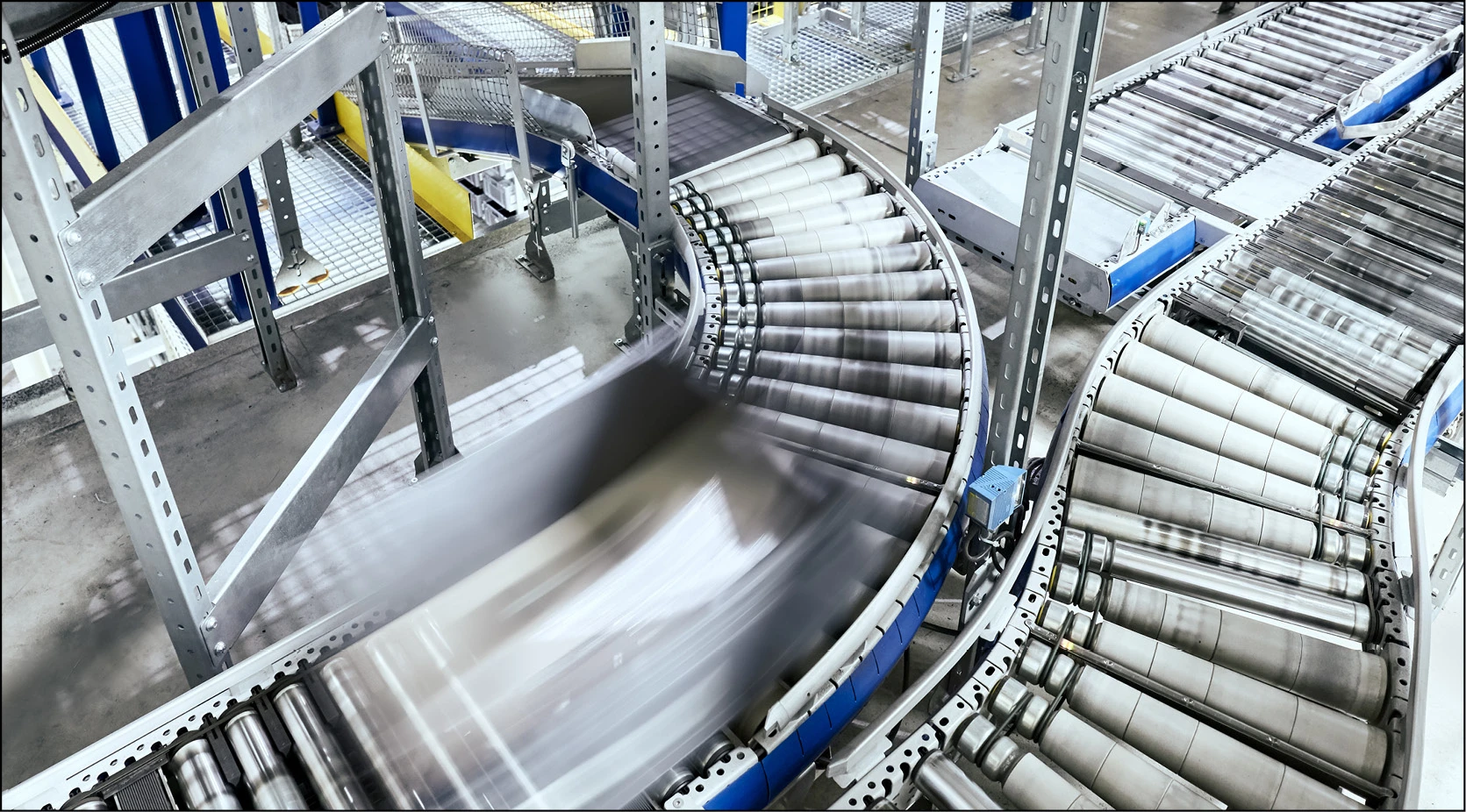
Optimizing quality checks on the production line has numerous benefits. Manufacturers can improve product quality, drive innovation, and address the root of product defects. Quality checks move upstream in your supply chain, catching defects earlier. The cost of quality control decreases, as does the aftershock of defects and compliance gaps.
When it comes to saving time and money, few activities can compare with production line quality checks. The standards you enforce can be the difference between happy customers and dissatisfied ones, and help you avoid the ripple effects of product defects: costly returns or chargebacks, damaged trust, and strained relationships.
What are production line quality checks?
Checkpoints that take place across the production line to ensure the product meets specifications and quality standards. Production line quality checks are important to identify and correct product defects upstream in the production process. The data gathered during the quality checks can be used to maintain limits of tolerance and reduce waste and re-work.
The emergence of digital, cloud-based platforms means production line quality checks can be optimized to allow you to take action in real-time and give stakeholders unprecedented leverage for quality assurance activities.
The cost of quality issues
The American Society for Quality reports that manufacturers spend between 15% and 20% of sales revenue on quality issues, though it’s not uncommon for that figure to spike as high as 40%.
That’s why optimizing production line quality control is such an attractive investment. You gain tighter control of your quality by performing checks at more points in your supply chain, while saving on human effort.
How does improving production line quality checks benefit you?
If you’ve read our blog posts, you’ll have heard of the 1-10-100 rule.
The rule goes like this: if the cost of preventing a quality defect is $1, the cost of fixing it will be $10, and if it reaches consumers, the cost will be $100. The message is that preventing quality issues is always the cheapest option.
1. Improve your production efficiency
Identify defects at the beginning of the production process when they’re still easy to fix. This means you won’t have to waste money and labor fixing the defect later, when it’s become bigger and costlier. That reduced rework translates to improved production efficiency.
2. Increase your return on investment
Minimize time and money by correcting defects in materials and products early on and accelerate time-to-value and maximize return on investment. Allocate the resources you’ve saved toward other important jobs and investments.
3. Encourage continuous improvement
Continuously improve production methods and standards. Enable your quality team to follow the same production check standards on the same platform.
4. Enable sustainability
Contribute positively to your organization’s sustainability metrics. Optimizing your quality checks results in fewer defects, which saves costs and decreases waste — all of which builds trust with your partners.
For vendors, sharing production milestones and results with your partners allows your business to operate at full scale. This means a higher level of compliance and transparency, which will strengthen your reputation and keep buyers returning.
How to optimize your production line quality checks
Here are four tips for making the most out of your production line quality checks with new technology for automation and performance management:
1. Choose configurable standards
To ensure efficiency in your quality checks, you’ll need a configurable standard for processes. This will help inspectors know how and what to inspect on the production line, and give you the flexibility to adapt to different product lines.
2. Consolidate your data
When quality data isn’t standardized and centralized, it’s a challenge to make sense of it. Ensure that quality production line data is collected in a standardized format and entered into a dedicated system that can aggregate and analyze it. This will allow the factory to analyze performance and make evidence-based decisions.
3. Use A.I. to improve quality assurance
Artificial intelligence (A.I.) has truly changed the face of manufacturing and represents an opportunity you can access through the incredible capacity of cloud-based SaaS platforms.
Once you’ve configured your current data and set up automations, you have the power to gather, sort, and analyze quality and performance data from suppliers and manufacturers, without the need for expensive analytics teams.
You can do this at various points in the production process, including on the assembly line so you’re able to identify quality trends and work to improve upstream root causes of defects.
4. Optimize your inspection process and workflows
It is essential to optimize the actual workflow for inspectors, which helps improve their efficiency and productivity, and there are several ways SaaS platforms can help you optimize workflows.
For example, mobile devices can be used for factory floor inspections with some solutions, which guide inspectors through the workflow to ensure no steps are missed — all while letting other stakeholders monitor their progress in real-time.
By using a cloud-based Quality Management System (QMS) you also have access to historical data that you can build upon to improve quality with every production round.
How Inspectorio can help
Inspectorio Sight standardizes production line quality checks, making it easy for your inspectors to meet quality standards.
By making the inspection process transparent and alerting you to problems immediately, you can quickly move inspections further upstream to catch defects earlier in the production process.
Inspectorio Sight’s powerful software and A.I. gathers your quality performance data from the production line and identifies recurring defects early on, preventing the cost of defects in your finished products because of an ineffective inspection. It also makes implementing improvement plans quick and scalable, while making it easy to analyze performance.
To find out more, contact our team today.