How Vera Bradley Boosts Efficiency with Quality Self-Inspections
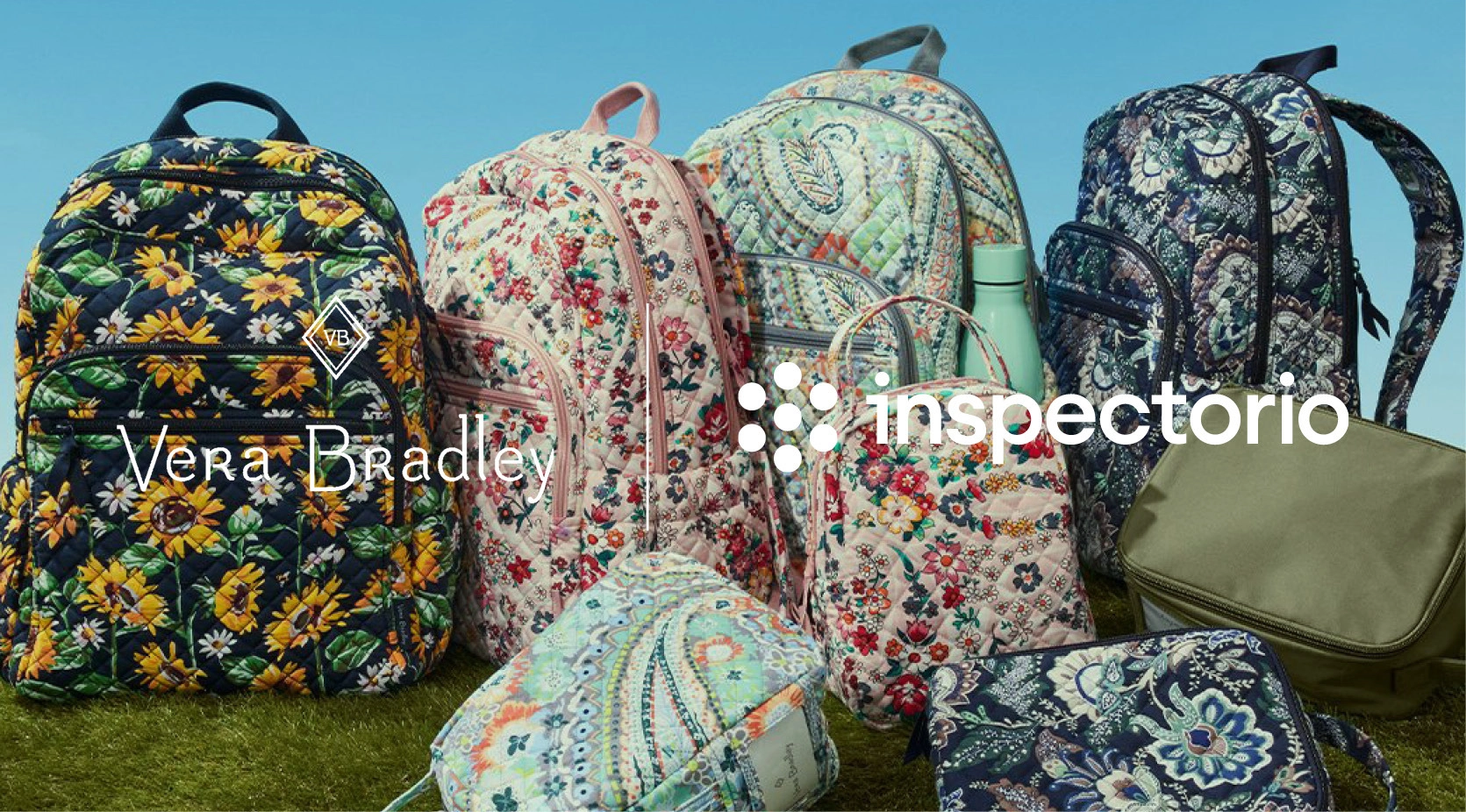
The case studies mentioned herein were conducted using our earlier individual solutions: Inspectorio Sight (now Quality Risk Management), Inspectorio Rise (now Responsible Sourcing & Compliance), and Inspectorio Tracking (now Production Management). Inspectorio transitioned to a unified platform approach, enhancing and interconnecting these solutions under the Inspectorio Platform to better serve our customers. Click here to learn more about the Inspectorio Platform.
Inspectorio is transforming how Vera Bradley manages product quality and compliance across its supply chain, according to Sourcing Journal.
About the Company
Vera Bradley is a global designer of women’s handbags, luggage, and accessories. Established in 1982, the brand is known for its iconic patterns and original designs.
Challenges
Vera Bradley’s quality operations were manual and reactive, causing inefficiencies, defects, wasted resources, and poor-quality goods.
- Pen-and-paper inspections caused long lead times, with manual analysis of reports and data.
- Communication via email and static documents led to slow response times, limiting visibility into real-time inspection results and insights.
- Policing supplier production facilities was laborious and expensive, damaging relationships with factories.
Solution
To overcome the quality challenges, Vera Bradley turned to Inspectorio to implement a self-inspection program.
Centralized platform
All quality and compliance processes are digitized in one place, allowing for better collaboration between Vera Bradley and their suppliers. No more inconsistent standards, missed emails, and static or delayed reports.
Real-time data analytics
With Inspectorio’s machine learning and AI-driven analytics, they can quickly spot the root cause of production issues, rectify them faster, and gain actionable insights to improve quality standards. Dreaded defect and remediation cycle times are no longer an issue.
Mobile app
With Inspectorio’s user-friendly app, inspections are easier than ever. Inspectors access data, click and upload photos, highlight defects, and submit reports directly from the factory floor.
Results
Vera Bradley has significantly improved quality and compliance since adopting Inspectorio’s digital solution.
“One of the biggest gains from using the Inspectorio platform is the ability to identify trends with respect to factories, defects, inspectors, etc., allowing us to be more proactive than reactive to issues.”
– Rory Geiger, Director of Global Quality and Compliance at Vera Bradley
One-click reports
Manual report generation went from days to seconds, enabling Vera Bradley to respond faster and better address supplier issues.
Real-time insights
With real-time data access, Vera Bradley has gained visibility into factory compliance and can quickly act on deviations from their standards.
Improved relationships
Vera Bradley enjoys more productive relationships with suppliers due to their improved quality processes and timely follow-ups. Both parties have a deeper understanding of each other’s needs and are better aligned to achieve them.
Standardized workflows
Standardized quality workflows, defect lists, and AQLs are now the norm across all of Vera Bradley’s factories and vendors, bringing consistency to the process and minimizing non-compliance risks.
Empowered factories
The self-inspection program enables Vera Bradley to identify top-tier and underperforming factories. Factories with good scores are rewarded with more autonomy, and those that need improvement are incentivized to improve their performance.
“The savings, or benefits, for us in allowing factories to perform self-inspections really stems from the ability to improve our resource allocation to higher-risk and underperforming factories.”
– Rory Geiger, Director of Global Quality and Compliance at Vera Bradley