4 Ways to Improve Corrective and Preventive Actions (CAPA)
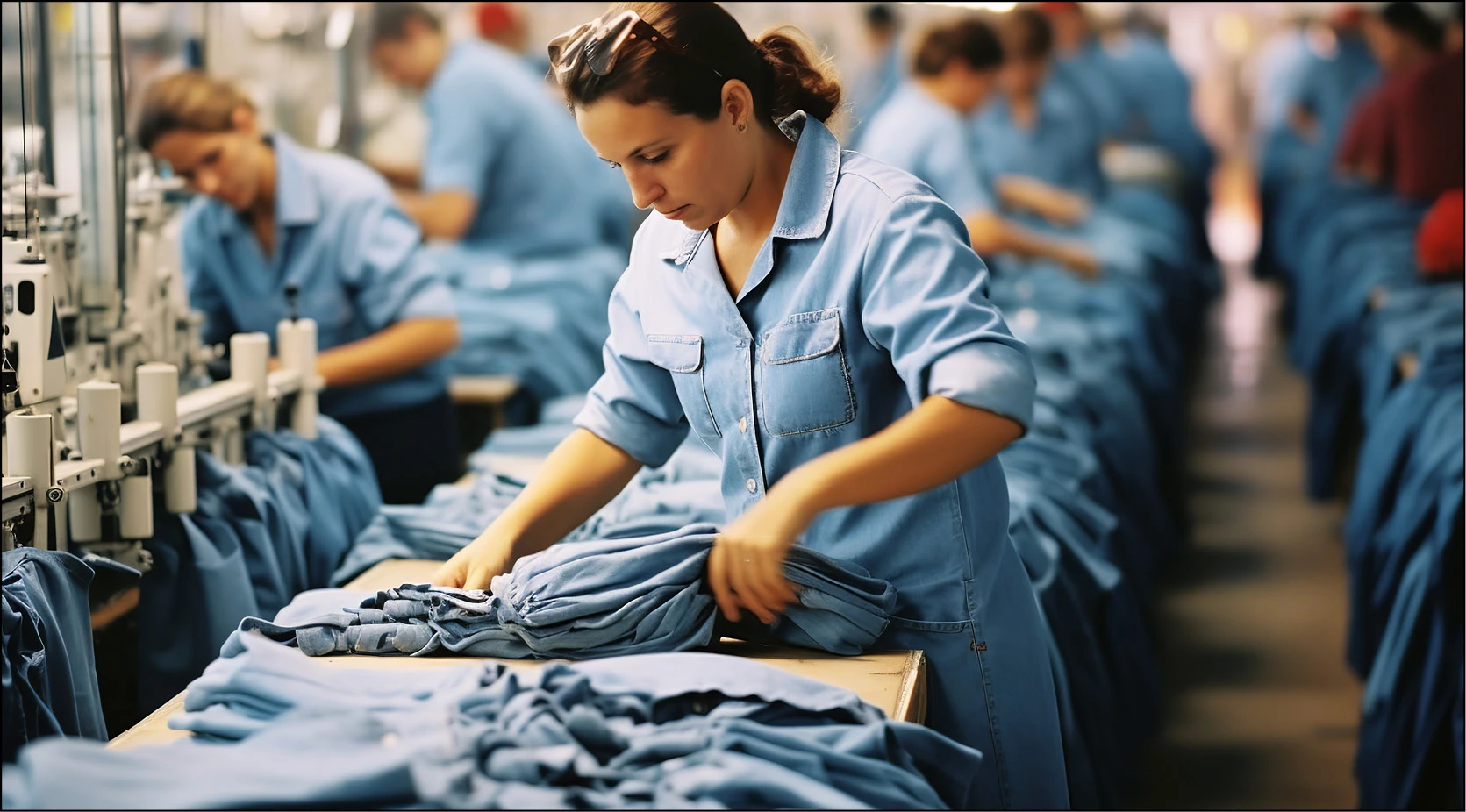
Written by Nick Inzeo
Corrective Action and Preventive Action (CAPA) plans happen all the time because they’re incorporated into the production process and are considered standard practice in the manufacturing industry. However, because they’re considered to be standard practice, some organizations have become less rigorous with the implementation of their CAPAs.
What is a CAPA?
CAPA stands for Corrective Action and Preventive Action. The CAPA process represents what has to be done to address and prevent root cause issues that lead to problems from happening again in the manufacturing industry and other industries.
Corrective Action (CA) is the first step designed to stabilize production, so it’s an immediate action to stop a problem from continuing during the production process.
Preventive Action (PA) is used to improve processes to help prevent the same issues from happening again, so it’s a long-term action that’s used to update processes to ensure preventative measures are in place to mitigate the risk of the same problem reoccurring in the future.
While the Corrective Action (CA) has the main goal of solving issues as they arise, the purpose of the Preventive Action (PA) is to address and eliminate the root causes of the problem(s) while committing to improve the production process long-term. For this reason, finding the root causes of issues is one of the most important steps in the CAPA process.
There will be defects in every manufacturing production, especially if there are manual processes involved. Because of this, CAPA will always be relevant and play an important role when striving to achieve closed-loop performance management.
To help you improve your CAPA processes, here are four ways you can improve how you use CAPA to ensure you’re getting the maximum value from the framework.
4 Ways to Improve the CAPA Process
1. In-Depth Analysis of Root Causes to Generate the Impact
To improve their CAPA process, an organization needs to first start with an in-depth root cause analysis. There are four frameworks one can use to do an in-depth root cause analysis:
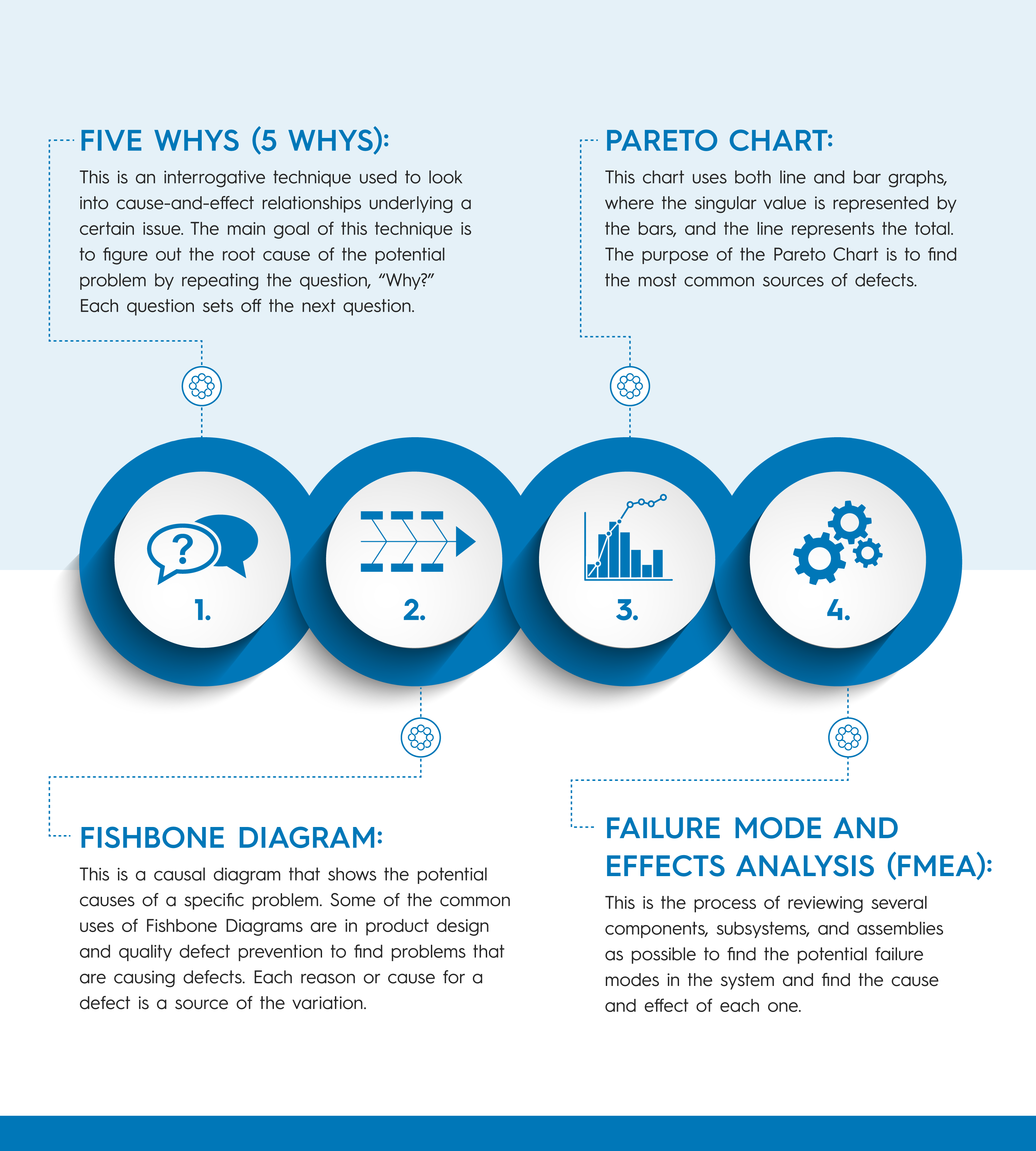
After using one, or all, of these four frameworks and figuring out the root cause of the potential problem, you’re able to learn from it and implement preventive actions that will help improve the manufacturing process in the long run.
Getting the root cause analysis right in the beginning is important for implementing an effective CAPA. A CAPA action plan is dependent on a good root cause analysis. Organizations that fail to implement one can expect recurring issues and problems.
To effectively perform a root cause analysis, you must:
- Define the problem
- Understand the process
- Identify potential causes
Again, you can use one of the four models listed above to do a root cause analysis that will help you better understand what is going on with your process and why the issues are occurring.
2. Involvement of the Right Stakeholders
After finding the root cause of the problem, you must get the right stakeholders involved and get their support, so the CAPA isn’t just written on paper and forgotten. You need to ensure planned actions are executed.
When you get the right decision-makers and managers involved, the company can implement the preventive actions they define during the root cause analysis, ensuring the implementation of long-term preventive actions.
The stakeholders who need to be involved in the CAPA meetings are:
- Production managers – These are the people who are in charge of the product quality.
- Upper Management – These people influence others to adjust the production process as the PA suggests.
Having production managers and upper management involved means that you have the people who are empowered and can make an impact involved in the CAPA meetings. This means they can learn about what needs to be fixed or implemented and find ways to do so by finding funds or finding ways to add the solution to the production process.
3. Create a Balance When Implementing Frameworks to Create an Impact
Creating the right balance when an organization implements frameworks can be difficult, especially considering cadence depends on the organization and its working model.
Implementing CAPA can be a time-consuming project. Because of this, it’s wise to find a way to make CAPA work with the organization’s cadence.
It’s highly recommended when organizations implement CAPA to aggregate information so they don’t have to do CAPA for every single production. Master CAPA is a great way to aggregate the findings of several productions to find challenges and issues.
To implement master CAPA, you need to aggregate all learnings from past CAPAs into one specific area of improvement. Then you’re going to look at the aggregated data points as opportunities to learn to implement a solution early into the production process – the goal is to optimize production process quality.
By using aggregate CAPA data, you can identify areas requiring continuous improvement.
Doing this can also be a great way to ensure your CAPAs are implemented correctly; this will also make it easier to follow up on the CAPA process in the future.
4. Create Traceable Discussions and Commitments
You need to ensure all CAPA project plans are traceable. This means keeping a log of all discussions and activities that take place.
This helps create accountability and drive the CAPA forward, so it’s not just an idea on a piece of paper.
When you’re doing this, you need to make sure you’re establishing owners, timelines, and milestones so you have a way of looking back and seeing if the CAPA was successful or not.
CAPA can require multiple steps, and because of this, it needs to be continuously monitored.
How to Implement CAPA Efficiently
When trying to implement an effective CAPA system, it’s important to recognize the power of technology and its role in the efficiency of CAPAs.
Technology makes it possible to bring all stakeholders involved in the CAPA together into one collaborative space without them having to relocate. This ensures everyone is on the same page at all times because they’re always included in the discussions and can help improve accountability while providing real-time updates on the CAPA projects.
This is important because when everyone is on the same page, the CAPA can move ahead without delays or issues. Plus, you can easily create traceable data of the discussions by, for example, recording them.
Remember, traceability is one of the four ways to improve the CAPA process.
Technology also allows organizations to see historical data, which is critical in relation to aggregate CAPA.
Seeing the historical data on defects in a production process helps you see recurring issues and allows you to create solutions for those recurring issues.
You can also use historical data to keep track of the facilities, and it helps you realize when a recurring issue starts happening again in the production process.
While the above points are important, the most important point is the that trends you find in data tell a story.
Using technology allows you to use those learnings from production process outputs and apply the learnings to the start off the production.
If you remember the closed-loop performance mentioned earlier in this article, this is how it’s achieved.
Once you’ve completed a CAPA, you can use the data from the pre-production coordination to win by design. This is essentially closing the loop.
Conclusion
During the production process, there are countless issues requiring correction and prevention. This creates an opportunity to leverage CAPA and engage in a process of continuous improvement.
Good quality control means you’re always catching and correcting problems that occur and potentially create an undesirable situation.
However, good quality assurance means you’re diving deep into the root cause of the problem and process to mitigate the risk of the issues and challenges from happening.
This is an important distinction because you need both to be successful. Otherwise, if you’re only focused on one, you could miss something major in your production process that could fix the problem.
CAPA management needs to be considered a proactive process instead of a reactive process for it to be effective. While CA is more reactive because it aims to correct a problem immediately after it occurs, PA is what really makes the process proactive.
PA ensures the problems that occur during production don’t happen again because you’re using the quality data you’ve gathered using technology to find a story.
Once you’ve uncovered the story, you can use those learnings to go back and implement improvements from the beginning of the production process – once again, achieving closed-loop performance management.
When used correctly, CAPA can be an incredibly helpful tool that allows you to take the issues and challenges plaguing your production processes and find solutions that are both immediate and long-term.
Corrective Action Preventive Action is a great way to solve any problems that may occur in your processes, as long as you understand how to implement it effectively.