Inspectorio Wins 1st Place at Coresight Research Innovator Showcase
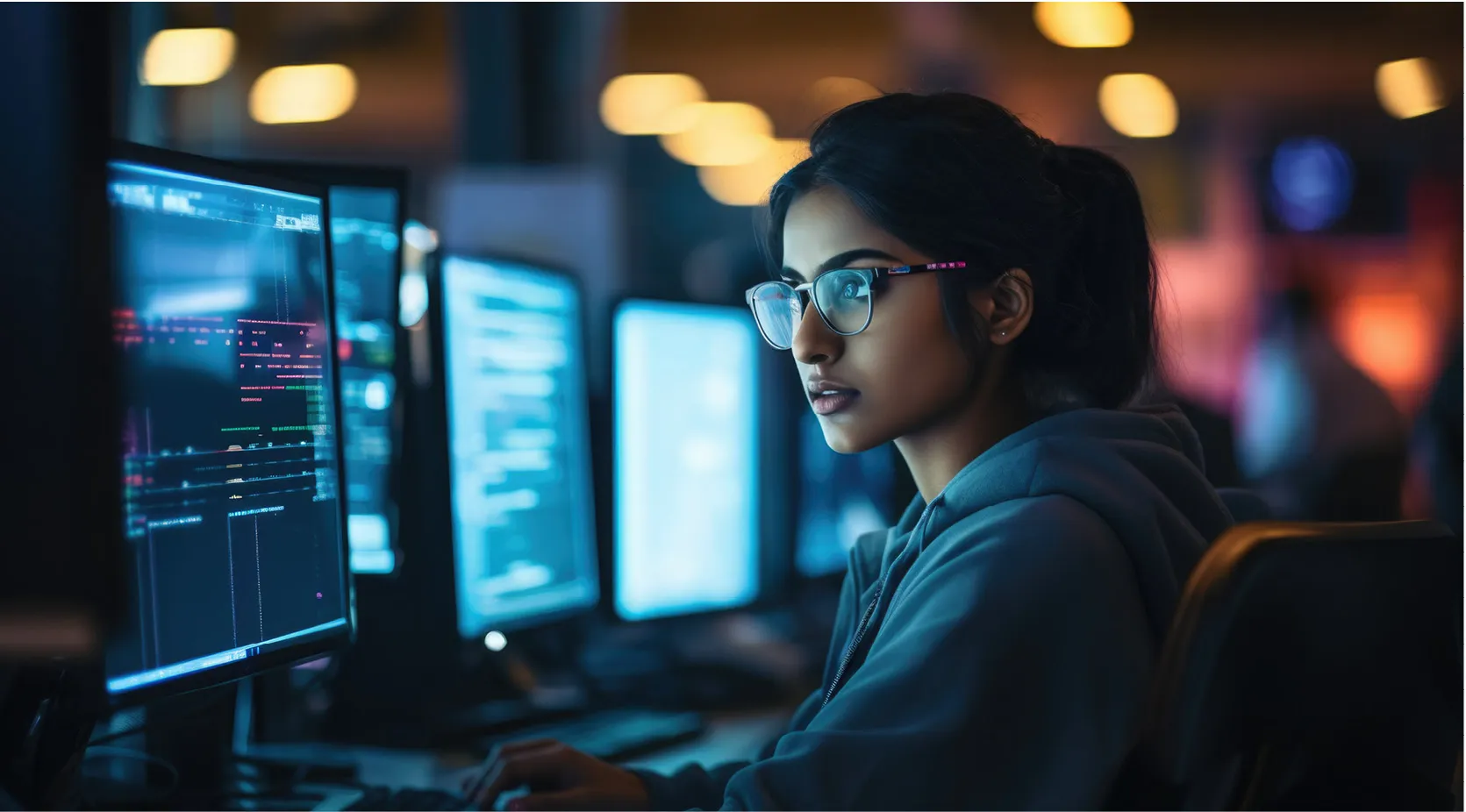
We are honored and humbled to have won 1st place at Coresight Research’s recent Innovator Showcase, where Inspectorio, alongside other growth stage technology companies, presented solutions for the most pressing problems facing the retail industry today.
Pre-event Q&A with David Klein, President and Co-Founder of Inspectorio, and Deborah Weinsberg, CEO of Coresight Research.
On February 18th Coresight Research hosted its first pitch series event of the year, featuring 5 growth stage technology companies bringing innovative solutions to market for the retail industry. The COVID-19 pandemic has dramatically changed the face of the retail and supply chain industries, accelerating the shift to technology adoption for many retailers – the participating companies offered solutions in various areas of retail, such as digital design, marketing tools, merchandise tracking, supply chain optimization, and return reduction.
A judging panel of retail and technology leaders presided over the event and evaluated each company on the same set of criteria, including market opportunity, confidence to invest in the company, trust in the team, business model feasibility, and potential to scale.
This panel included:
- David Matthews, Managing Director at RevTech Ventures
- Robert Mills, Chief Technology, Digital Commerce and Strategy Officer at Tractor Supply Company
- Melissa Campanelli, Co-founder at Women in Retail Leadership Circle.
Inspectorio is delighted to have been honored as the winner of the showcase. David Klein, President and Co-Founder of Inspectorio, while speaking at the event said,
“This is extremely exciting and a huge honor. From the very beginning of founding the company we’ve had a consistent mission of truly bringing the interconnected nature of our supply chain into a digital solution that reflects that interconnectedness, and that allows factories, vendors, brands, and retailers to truly cooperate, maximize their use of resources, and start collaborating in a pre-competitive environment. It’s amazing to have this recognition. We will continue to push forward in this journey to shape and make the industry more transparent and more efficient”.
The Retail Technology Revolution
Even before the beginning of the pandemic, the retail industry has been tapping into the potential of digitization; however, as we move in to 2021, innovation and the adoption of new technologies is becoming essential for all retail and supply chain organizations.
“The accelerated digitalization and uptake of new technologies can help businesses thrive in the new normal,” explained Coresight Research.
Digitalization enables companies to become more agile, and pivot quickly in a changing environment, in addition to building a powerful competitive advantage that will be essential to lead future-ready companies.
Technology spending in the retail industry is predicted to increase even further in 2021 and beyond. According to Gartner, “spending is expected to rebound to a 3.9% CAGR to reach an estimated $279.9 billion by 2024.” This shows that retail companies are investing heavily in technology solutions, recognizing that technology can help them better serve their customers.
Some of the most prominent trends in retail tech are focused on increasing operational efficiency by leveraging AI, IoT, and cloud-based solutions across diverse areas, such as product development, customer engagement, marketing and merchandising, and supply chain management.
McKinsey explains that most supply chains “run on old principles and processes,” and the supply chain operating model must be upgraded to meet the demands of the market in the digital age. Adopting new technologies in the supply chain can help companies keep up with consumer demands, minimize costs and maximize productivity, and leverage advanced analytics for efficient design and planning.
In the case of supply chain management, Inspectorio is leading the charge when it comes to improving operational transparency and efficiency, and ultimately reshaping the way in which the global production network operates.
About Inspectorio
Inspectorio is an end-to-end performance management platform for quality and compliance. Its aim? To transform the global production chain into an interconnected, empowered, and sustainable production network. In this way, Inspectorio’s network platform connects the global production chain, building data-driven collaboration amongst stakeholders, and bringing unparalleled visibility into the production of goods across the globe.
David Klein, Inspectorio’s President and Co-Founder, explains that production across the global supply chain has traditionally run on manual and disconnected processes, which prevent collaboration and hinder efficiency. The relationship between retailers, vendors, and factories is linear, and the coordination that needs to take place between these stakeholders to ensure the successful production of goods is currently happening in silos.
Manual systems do not allow organizations to build resiliency across their supply chains, something that is accomplished by:
- standardizing processes
- gaining real-time visibility over the state of production
- utilizing data to obtain actionable insights.
The consequences of running an analog supply chain (as shown above) can be substantial for global organizations, as there is increased demand from the market to deliver new and better products quickly. Future-ready supply chains must be designed to be fast, innovative, and resilient.
Inspectorio’s digital platform is changing the way in which global production chains operate. The relationships between brands, retailers, vendors, and factories translate to a digital network, where data is collected in real-time and used to develop powerful insights for decision making and continuous improvement.
With a digital tool like Inspectorio, organizations are able to digitize and standardize their quality and compliance operations, with the goal of automating and optimizing processes across the production chain.
As Klein explains, this kind of system can bring great benefits such as “higher quality, less returns, and more compliance for retailers and vendors.”
The optimization and automation of supply chains can dramatically reduce overhead costs, as modern technology solutions powered by artificial intelligence can help organizations predict and prevent quality and compliance issues before they occur. Connecting all stakeholders, data and processes in a single, centralized platform enables organizations across the global supply chain to truly collaborate, enabling them to be more resilient, and more agile.
This ability to help organizations to become more resilient and agile in their operations has been demonstrated in practice during the COVID-19 pandemic, as Inspectorio enabled organizations to continue operating remotely, even when competitors’ quality and compliance operations ground to a halt.
Inspectorio Sight (designed to digitize, automate and optimize quality operations), enabled our clients to empower their vendor and factory partners to conduct self-inspections remotely and ship on time in spite of the pandemic restrictions.
While the Inspectorio Rise platform (used to standardize, execute and monitor compliance operations across supply chain networks), empowered organizations to conduct health and safety self-assessments, allowing facilities to safely reopen in accordance with COVID-19 H&S measures.
“The way in which you build a resilient supply chain is by getting a pulse on what is happening on your factory floors, something that allows you to become nimble and agile in how you operate and move”, said Klein.
Inspectorio’s technology provided organizations with a means to find that pulse, and to keep their business operations alive during the height of the pandemic crisis.