Top KPIs for Data-Driven Quality Management
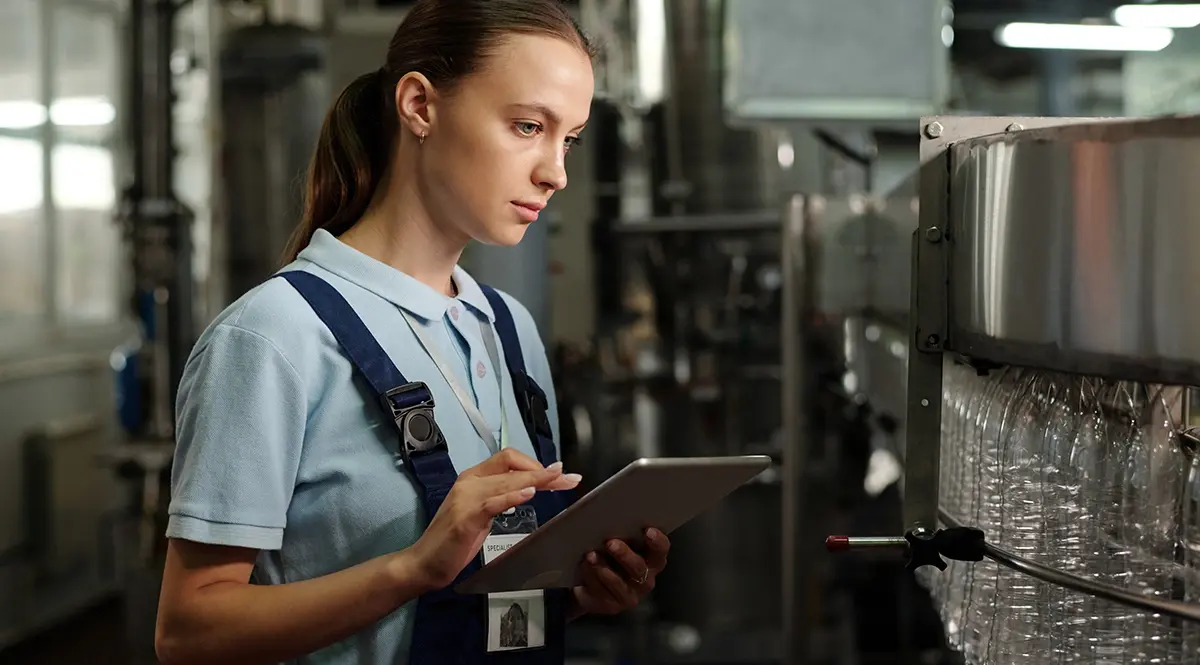
New digital platforms have revolutionized quality management. Though such platforms make quality more intuitive than ever before, using data to improve quality management across your supply chain is a continuous process — and one of the most important steps is identifying your top key performance indicators (KPIs).
An expert on this topic is Jose Martinon. He serves as Director of Quality Assurance for Barco Uniforms, one of the world’s leading providers of professional uniforms. Below we summarize his insights from a recent webinar.
But first: What does data-driven quality management mean?
“For me, it’s reducing that subjective element of the equation,” Martinon says. “That means reducing the guessing. Then comes the ability to collect raw data and turn it into beautiful analytics, then being able to use those analytics to drill down to the root causes of issues and make better decisions.”
Below we look at which KPIs Barco Uniforms is tracking and how these KPIs are helping them improve data-driven quality management.
1. Defect Trend & Defect Percentage
“Defect Trend and Defect Percentage are among the most vital analytics that I use,” says Martinon. “Once I see a defect percentage that’s higher than the norm, I have to bring it down and understand where it came from.”
Defect Trend and Defect Percentage allow Barco to do this by showing each defect percentage on random inspections, inspections in the production line, and final inspections. If there are any abnormalities, the intuitive chart makes it easy to spot them and understand where the defects are coming from. Martinon uses this to drive continuous quality improvement among factories.
The first step in driving quality improvements is to understand your overall defect rate. The second step is to understand which defects are actually contributing to it and to dig deeper to understand the root cause.
With regards to industry standards, Martinon says he strives for a 0% defect rate. “I know that’s a challenge, but I always want my defect rate this year to be less than last year. The ultimate goal is to approach zero.”
Achieving this goal is only possible with a trustworthy, centralized source of data that shoulders the burden of analytics and gives you data insights for decision-making.
2. Defect Breakdown Chart
The Defect Breakdown Chart helps you understand your overall defect rate, as well as which defects are actually contributing to it. With this information, you can efficiently uncover the root causes of the defects and take action to solve them.
Martinon remembers the importance of implementing standardization across Barco’s supply chain when he began his job there: “When I started, I found that training was necessary because there was no standardization — everybody had a different concept of critical inspection protocols such as whether a defect was major, minor, or critical.”
Martinon began by classifying what each of these defect categories meant. Once all inspectors were aligned, Martinon could use the automatically generated Defect Breakdown Chart to identify where the issues were originating.
For instance, if a defect stemmed from textiles, they could focus corrective efforts on the mill rather than on the assembling of goods. This ability to zero in on the actual source of defects allowed Barco Uniforms to quickly take meaningful, high-value actions in their quality operations. Their supply chain is now set up for continuous improvement.
3. Product Line & Category Summary
New capabilities are only as good as their results. How can you actually use increased visibility and data analytics to drive change?
For Martinon, the Product Line & Category Summary provides a concrete example of bridging the gap between capabilities and improvements. Inspectorio’s platform alerted him to an issue with batches. Using analytics and real-time communication with the factory, Barco Uniforms was able to zoom in on the problem until they found its source: the entire issue stemmed from a mere 1/16” error in the component’s template.
Neither inspectors nor the factory’s technicians regarded this as a significant mistake, so it continued to be missed. Barco provided the necessary training and corrected the issue — and they were able to do this remotely, using software-generated visibility.
This is just one example of how a network platform like Inspectorio allows you to locate defects and work with suppliers to drive meaningful change on the factory floor.
4. Performance Ranking
It’s important to know who your best-performing factories are. With the Performance Ranking feature, your supply chain partners are ranked according to a risk score created using artificial intelligence (A.I.) analysis.
Barco rewards its highest performers by allowing them to conduct self-inspections, in which case Barco no longer regularly sends its own inspectors to the factory.
On the other end of the spectrum, Barco handles low performers not by removing them from their supply chain, but by helping them improve with targeted training, corrective and preventive actions, and other continuous improvement efforts.
Further insights
The following were questions posed by the webinar audience. This is Jose Martinon’s advice:
What methods and tools do you use to improve these KPIs?
The earlier in the process you can catch issues, the cheaper they will be to resolve. This means moving from reactive to preventive methods.
While conventional quality assurance leans heavily on in-line and final inspections, tools like Pre-Production Meetings (PPMs) and real-time information are extremely important to fix issues at the beginning of the process. Tools like Inspectorio Sight can help improve processes and identify trends with data.
How do you manage time and efficiency during your work?
Before using Inspectorio, Martinon said he wouldn’t receive a report until a week after the inspection. This is because inspectors took photos and worked with pen and paper, and then needed to transfer and upload these to an Excel sheet. Creating usable analytics out of these reports required 3 to 4 more days of work.
A digital tool allows you to standardize your processes. Even though this may require systemic changes in your supply chain, the overall efficiency of the system improves significantly. This saves tremendous amounts of time overall, while also increasing the accuracy of data and the quality of decision making.
How do you usually select the “K” of the “KPIs”?
The “north star” metric for Martinon is the 12-month rollover Defect Percentage. Ultimately, all categories of defect rates — major, minor, critical — all roll into that KPI.
“Nothing is perfect,” Martinon says. “This product is not being made by a machine; it’s being made by humans. So, you’re going to have an allowance for defects.” This KPI helps Barco calibrate and stay ahead of undesirable developments while optimizing the performance of suppliers.
How often do KPIs need accessing and reviewing?
The most important question to ask is, “what will this KPI help my team change?” If you can’t answer that question clearly, it may be wise to consider other KPIs. In Martinon’s case, he reviews Barco’s KPI choices monthly.
Watch the full webinar to find out more about how to build data-driven quality management with the right KPIs and technology!
Click here to watch now!