Why Vendors Need Internal Quality Management: Benefits, KPIs, and Tips
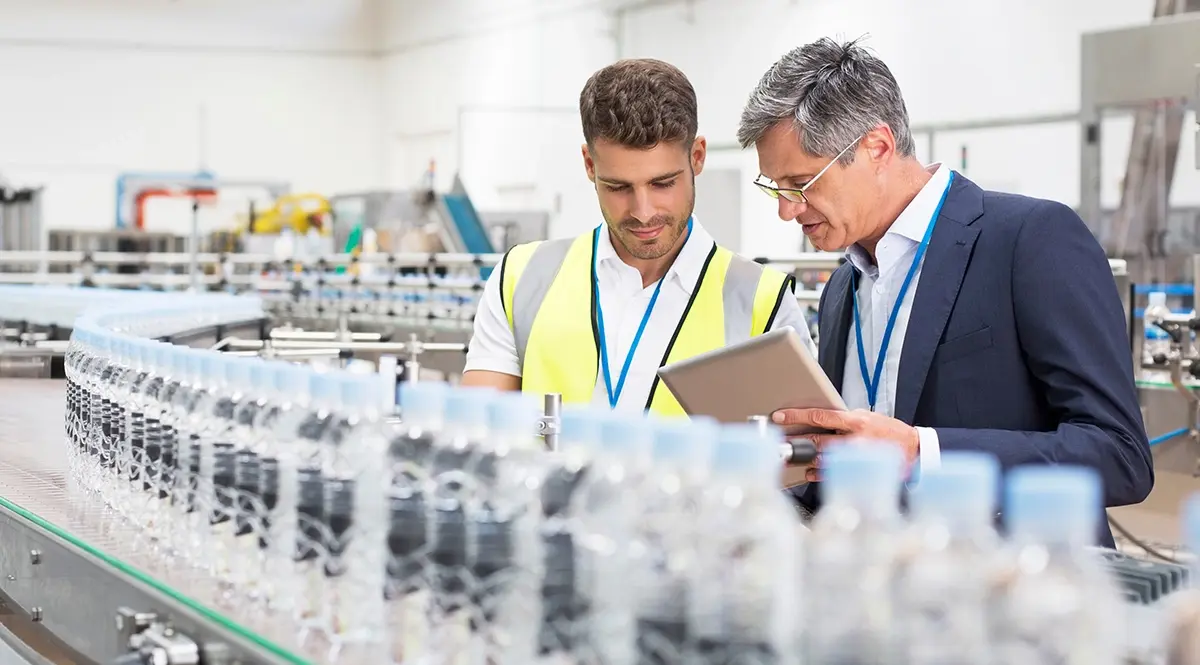
We tend to associate quality management with brands and retailers — but what about vendors?
Quality is not (and should not) be seen as a policing program enforced by brands. Rather, it is a tool for all stakeholders to increase their revenue, customer base, and productivity. For vendors, it represents an opportunity to build better buyer relationships by reducing product defects, reducing wasted time, material, and money while improving reputation and business.
The problem? Most vendors don’t have their own quality programs.
Below, we look at how to find the right internal quality management solution (QMS), which key performance indicators (KPIs) to track, and how owning your QMS can boost business.
What is a QMS?
A quality management solution (QMS) allows different organizations like brands, factories, and vendors to standardize processes and product parameters, making producing on-spec, defect-free products easier.
There are a few good ones, a few bad ones, and a lot more that simply missed the boat on opportunities to innovate. In general, you’re looking for:
- Real-time data: Your QMS must deliver data in real time to help you prevent problems instead of doing damage control.
- A centralized network platform: This connects you to the rest of the industry, letting you set more effective benchmarks for your operations while anonymizing data.
- Robust analytics: Particularly when powered by artificial intelligence (AI), in-suite analytics instantaneously unlock insights that would otherwise take significant time to identify.
- KPI tracking: Your QMS should make tracking KPIs at a glance easy.
Why should vendors have an internal QMS?
Vendors benefit just as much as brands and retailers by owning their own QMS. These benefits include:
Improved product and service quality
Improving product quality starts with the ability to monitor and collaborate with suppliers. An effective QMS centralizes all inspection activity, stakeholder communications, reporting, and metrics to one consolidated platform. Access all important information from your dashboard.
Reduced human error
Reduce the likelihood of human error by automating every possible workflow, leaving only high-value processes for you and your colleagues to complete. Automation takes care of tracking, calculating dates and renewals, assigning documents, and scoring risk and performance metrics.
Better risk management
Save on compliance and audits with end-to-end risk management. While Inspectorio Sight digitizes quality management, Inspectorio Rise digitizes compliance for comprehensive risk mitigation across your suppliers. Collaborate efficiently in real-time, monitor progress against benchmarks, take a data-driven approach to solve challenges, and demonstrate progress to the public and regulators.
Savings on document printing and storage
Companies spend as much as 3% of their revenue on printing, filing, and storing paper — all for a system that is inefficient and prone to data loss. A product like DocuFlow digitizes all documentation while keeping it securely on-platform.
With DocuFlow, you can automate all review and approval tasks and alerts, reducing manual work and freeing up bandwidth for other activities. Improve accountability and dramatically cut down on the amount of manual work required for due diligence and document control.
Better collaboration
Communication silos are responsible for great losses among companies around the globe. By bringing all stakeholders into the same virtual room — and eliminating fragmented channels like email and messaging apps — vendors can bring revolutionary efficiency to their communications. On-platform communication increases visibility and enables more streamlined management.
Stronger relationships with brands and retailers
When brands and retailers see their vendors performing internal quality management, they see two things: better profit margins and a more reliable business partner — or “team-mates, not vendors,” as Manufacturing Digital puts it. Gone are the days of finger-pointing — all data is now available for everyone to see. That makes for better relationships and a better pitch to new customers.
KPIs of a vendor’s internal QMS
The KPIs you choose to track will depend on the unique circumstances of your particular business. However, based on historical data from over 8,000 companies in the Inspectorio network, we can point to several KPIs that stand out among our customers:
1. Defect rate
This metric helps you understand which kinds of defects are occurring most frequently and are likely to do so in the future. Even more importantly, this KPI tells you where you can expect to find different categories of defects and how many you can expect per unit.
Calculated as the ratio of the number of defects to the number of inspected units, Defect Rate provides a reliable index of how your quality operations are progressing. Use Defect Rate as a baseline for your decision-making in gauging the success of a production strategy.
2. Productivity
Maximizing the productivity of your suppliers and internal processes is crucial to allocate resources effectively. Productivity gives you a measure of whether your production strategy is working on the ground.
Remember not to treat an internal QMS as a plug-and-play fix for your operations. It is a framework to optimize your processes, requiring adjustments as you find the right fit.
3. Compliance
Compliance helps you track your company’s ability to mitigate financial, reputational, and operational risks across numerous suppliers. From workers’ rights to environmental regulations to ESG, Compliance can be a proxy for general sustainability, an important metric in today’s global market.
4. On-time shipments
Tracking on-time shipments helps you uncover deeper, less-obvious truths about your partners, such as whether they are maximizing the capabilities of their production facilities and which product lines are causing issues.
How to implement an efficient internal QMS for vendors
A robust QMS has the ability to transform your company. To ensure you are getting the most out of your investment, pay attention to the following five areas:
Centralization
A centralized platform makes each piece of data more valuable because it puts it in communication with every other piece of data being collected on the platform. Leverage centralization to root out and eradicate silos, as well as to provide a fresh start for strained relationships with suppliers.
Standardization
“In an industry where lean, fast, and transparent reign as the three pillars, standardization of the system is critical for high performance,” writes India Free Notes. Indeed, standardization is among the most powerful capabilities your QMS can offer, and you should take full advantage of it.
Compared with those that don’t have an optimization plan, 79% of companies using management solutions for their supply chains achieve higher revenue growth. Standardization allows them to cut costs in the supply chain while delivering more reliably to clients.
Automation
Delegate any and all repetitive tasks to your QMS software. Automate your CAPAs, bookings, and other workflows to eliminate manual work and improve efficiency and morale across your supply chain network.
Advanced analytics
“The shift to Quality 4.0,” writes Astrix, combines the core elements of quality with “analytics and data governance through the adoption of new technologies” like “artificial Intelligence (AI) and machine learning (ML).”
Advanced analytics replace expensive teams of analysts poring over spreadsheets with dedicated algorithms that mine past and present data for trends. These analytics then present the findings to you in a digestible manner so you can take the appropriate action.
Continuous improvement
Your QMS provider should continuously improve and update their solution with new capabilities while providing ongoing support to help you reach your quality goals.
Inspectorio’s modern QMS opens new doors for vendors
Inspectorio delivers all of the above capabilities and more, allowing vendors to extract maximum value from their existing supply chains.
Inspectorio Sight is an end-to-end quality solution that removes all barriers to effective collaboration between remote partners. Gain full visibility of your supply chain’s performance and achieve maximum operational efficiency.
For sustainability, Inspectorio Rise delivers real-time data from compliance audits while providing actionable insights to make your production chain more efficient and transparent. Reduce risk by staying ahead of all internal and external sustainability initiatives.
Contact us for more information.